1. Conveyed Items / Operating Environment
- (a) Check Conditions of Conveyed Items:
-
- - Outer Dimensions: Width (W) x Length (L) x Height (H)
- - Direction of Flow
- - Individual Item Weight
- - Shape & Material: Cardboard box, plastic case, wooden box
- - Floor Condition: Flat, uneven, protrusions present, flexibility when conveying using pallets
- - Amount of Conveyed Items: How many items will be loaded onto the conveyor?
- - Loading Method: How will items be loaded onto the conveyor (by hoist, crane, forklift, or by hand)?
- (b) Checking Operating Environment:
-
- - Temperature: Normal, Low, High
- - Humidity: Moistness, Dust
2. Selecting Roller Width
- (a) If the Conveyor is Straight:
-
Choose rollers that are at least 50mm wider than the conveyed items.
Overhanging conveyance is possible for items wider than the rollers if the base surface is flat and solid.Select rollers approximately 70%-80% of the width of the conveyed items.
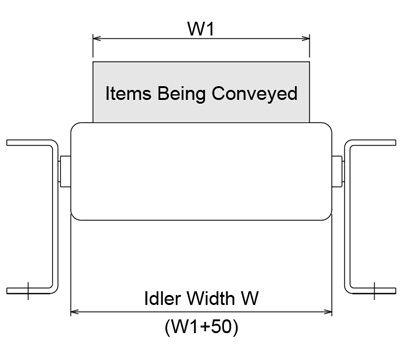
- (b) If the Conveyor is Curved:
-
For a curved conveyor with straight rollers, the roller width depends on the width and length of the conveyed items.
When selecting rollers, add at least 50mm to the item's width (as with straight conveyance), then add 15% of the item's
width to that sum.

If the conveyor uses tapered rollers, follow the guidelines for a straight conveyor.

- (c) If Conveying Pallets:
-
For conveying heavy items using pallets, we recommend using a multi-row (dual or triple row) conveyor depending on the
conveyed items weights.

3. Determining the Interval (Pitch) between Rollers
- - Please select a roller pitch (P) that ensures the base of conveyed items is supported by at least 4 rollers.

- - In some instances, the base of the items may not come into contact with the roller, this depends on the precision of
roller and frame finishing, as well as the condition of the item's base. Exercise caution when choosing the pitch and
strength of the conveyors.
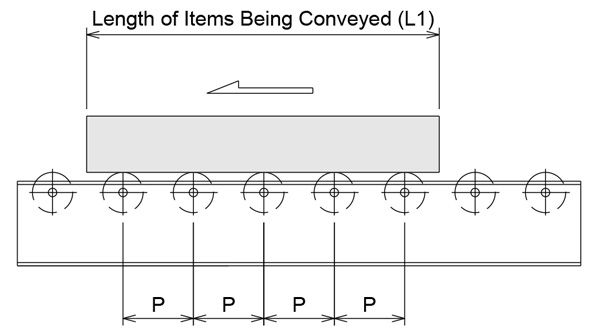
4. Selecting a Model
The strength required from each individual conveyor varies based on the material of the conveyed items and the impact
load when loading onto a conveyor.
- (1) Calculating the Load carried by One Conveyor:
- (a) If the base of the conveyed items is hard and does not change shape (metal, plastic, etc.)

- (b) If the base of the conveyed items is soft (wood, cardboard, rubber, etc.)

- (2) Impact Load when Loading onto a Conveyor:
- If there is an impact during loading, please multiply the load supported by one conveyor by the coefficient (N) provided below.
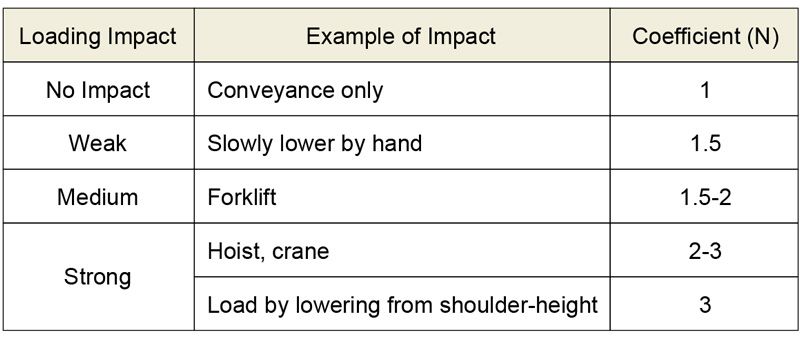
- (a) If the impact is distributed equally across all (at least four) rollers.

- (b) If the impact is concentrated on only one roller

- (3) If Using a Dual-Row Conveyor:
It is possible to convey up to 1.5 - 1.8 times more by increasing the number of rollers supporting the conveyed items, especially for heavy conveyance using a pallet or similar.
- (4) Strength per One Roller:

Once you have determined the load supported by one roller, please refer to our product specifications to select the most
suitable rollers and conveyors.
5. Setting Up Intervals Between Conveyor Stands
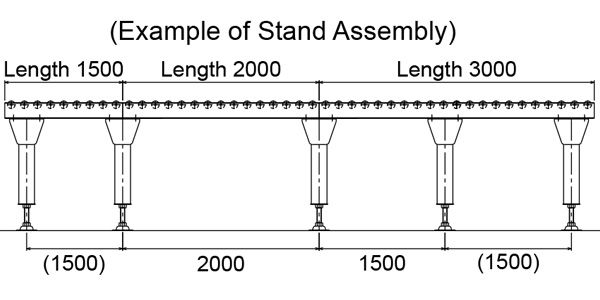
- - When mounting the conveyor to a stand, it's essential to consider the strength of the frame.
- - For straight conveyors, the standard is one stand at intervals of 1,500mm to 2,000mm.
- - For curved conveyors, the standard is one stand at the center of an angle of 45 degrees or more.
- - Determine the intervals between stands based on the frame strength indicated in the chart below, which has
converted the weight of conveyed items into weight per 1 meter.
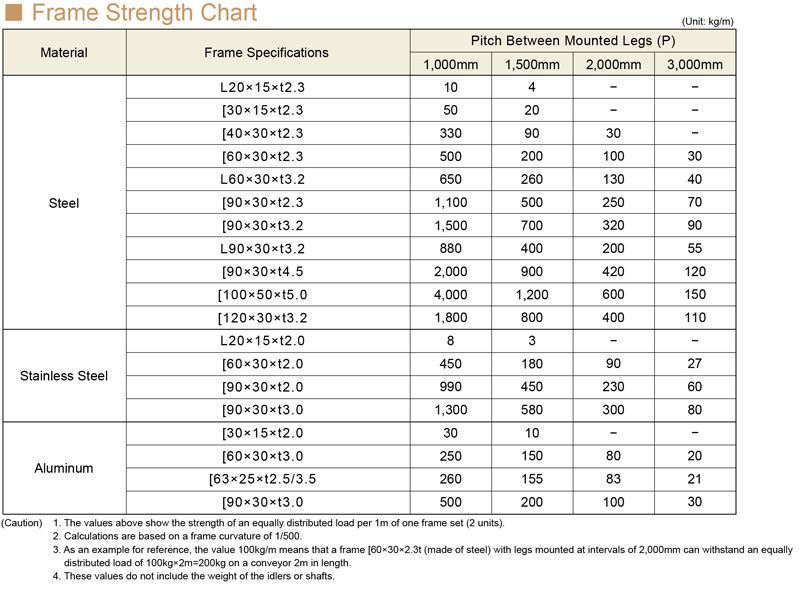
6. Determining Self-Incline:
- - Installing the idler conveyor at an angle (tilted) enables items to be conveyed by their own weight, a condition known as self-incline.
- - The degree of incline depends on factors such as the weight of the conveyed items, the condition of their base, external
air temperature and humidity levels. While an exact value may be challenging to determine, please refer to the chart
below for reference.
- - For conveying unusual items, testing is necessary. Please contact us for further discussion.
- - The degree of incline is also influenced by the type of bearing selected. If rollers share the same outer diameter and shaft
diameter, the degree of incline increases in the following order: precision-machined bearing > pressed bearing > standard bearing.
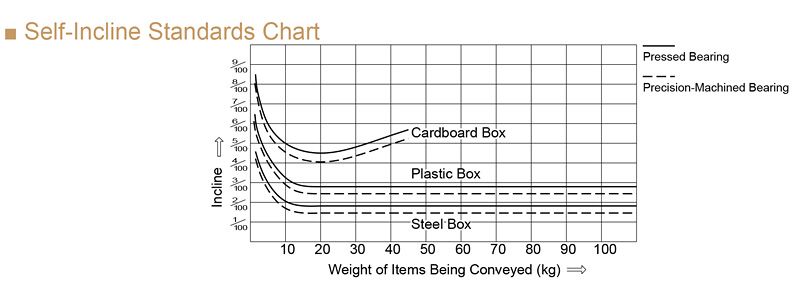